Supply Chain : Des métiers au coeur de la performance de l’industrie
Démarche globale portant sur les flux physiques, informationnels et financiers qui permet de synchroniser l’offre avec la demande.
Comprendre la Supply Chain | Des métiers transformés par un nouvel écosystème plus collaboratif | Des métiers transformés par la synchronisation globale et l’optimisation des flux | Des métiers transformés par le foisonnement technologique | Des métiers transformés par les attentes du client final | L’humain au cœur des transformations industrielles
Comprendre la Supply Chain X
NE PAS CONFONDRE LA SUPPLY CHAIN ET
- La logistiqueL’ensemble des activités relatives aux flux physiques (transport, manutention, stockage, emballage).
- La logistique industrielleLa part industrielle de ces activités : les flux physiques dans l’usine.
SUPPLY CHAIN
Une démarche globale portant sur les flux physiques, informations et financiers qui permet de synchroniser l’offre avec la demande.
Ensemble des échanges financiers : investissements machine, achat de matériels, salaires, recettes, …. pris en conscience de leurs impacts et en anticipant leur retour sur investissement.
QUI EST QUOI ?
- Précisions :
On parle de «Supply Chain Manager» en tant que fonction/métier et de «Supply Chain Management» quand il s’agit de pilotage de processus.
- Supply Chain Management, définition
C’est la terminologie anglaise qui est couramment utilisée pour la définir :
C’est la conception, la planification, l’exécution, le contrôle et le pilotage des activités de la Supply Chain avec un objectif de création de valeur, en construisant une infrastructure compétitive, en optimisant la logistique au niveau mondiale, en synchronisant l’offre avec la demande et en mesurant la performance globale.
(traduction de la définition officielle de l’APICS – association for Supply Chain Management)
SUPPLY CHAIN MANAGEMENT, fonction stratégique
C’est le macro-processus qui pilote et coordonne nombre de processus d’une entreprise industrielle : R&D I conception I achat I production I logistique industrielle I qualité I maintenance I transport.
Ce pilotage s’exerce au niveau stratégique, tactique et opérationnel. Il est animé par des personnes travaillant dans les métiers de la Supply Chain.
Historique de la Supply Chain
de l’intendance au Supply Chain Management en passant par la logistique
JUSQU'A 1940
- 19ème :
– Organisation de l’intendance : Depuis Alexandre Legrand, l’histoire de la logistique s’ancre profondément dans l’histoire militaire à travers l’organisation de l’intendance. Être capable d’acheminer, en temps et en heure et quelque soient les contraintes (éloignement, météorologie, complexité géopolitique,…), des hommes, des vivres et des munitions est une clé de succès pour toute campagne de conquête moderne. L’exemple des trains d’intendance de l’armée Napoléonienne en est une parfaite illustration. Le terme logistique apparaît pour la première fois dans le Traité sur l’art de la guerre du général Jomini (1838).
- 1930 :
– Fonction support dans une organisation taylorienne : Suite à l’organisation taylorienne des unités de production, la logistique est pensée comme une fonction support de la capacité de production. Elle est cloisonnée en un ensemble de métiers spécialisés que l’on connaît encore aujourd’hui :
prévisions I approvisionnements I planification I gestion des stocks I entreposage I conditionnement I distribution I transport I achat I gestion fluide
- 1940 :
– Recherche opérationnelle : L’organisation nécessaire à la logistique et à l’optimisation de l’effort de guerre de la seconde guerre mondiale pousse la logistique à s’adosser à une science très poussée : la recherche opérationnelle. La vision et les choix d’organisation logistique deviennent alors fondés par une logique mathématique de recherche d’optimaux. Le développement des sciences informatiques fournira un réel appui à cette évolution.
1960 > 1980
- 1960 :
Soutien Logistique Intégré-SLI : Le concept de coût de possession global (Life Cycle Cost – LCC) modifie la logique support de la logistique pour l’intégrer beaucoup plus profondément au sein de la chaîne de création de valeur. Tout d’abord utilisée pour des applications militaires, cette notion de Soutien Logistique Intégré a pour objectif, dès la conception du produit, d’en influencer la définition pour obtenir une meilleure disponibilité opérationnelle. La logistique commence à devenir transversale.
- 1970 :
– 3ème révolution industrielle : Basée sur le développement des nouvelles technologies de l’information et de la communication (micro-processeur, API,…), cette révolution marque le début de l’automatisation des lignes de production. La gestion informatique des données permet d’alimenter les progiciels de gestion de ce qu’on appelle alors la chaîne logistique.
- 1973 :
– Le code barre : Début de l’utilisation courante du code barre suite au brevet déposé en 1952. Cette automatisation de l’enregistrement des produits révolutionne la traçabilité des produits et sous-produits industriels. Associé aux évolutions de la 3ème révolution industrielle, cette innovation est la base du suivi de bout en bout de la chaîne logistique des produits industriels.
- 1964 -79 :
– MRP informatisés : Les premiers systèmes de gestion de production informatisés MRP (Material Requirement Planning) voient le jour en 1964 grâce à Orlicky pour le calcul de besoins matières. Ils évoluent progressivement vers le MRP II (Manufacturing Resources Planning) en 1979 pour intégrer la gestion des capacités et donc des ressources humaines. Cela permet ainsi une planification complète de la production, son suivi et l’anticipation des coûts associés. Le principe repose sur un équilibrage forcé des ressources et des besoins à chaque niveau.
- 1980 :
– Juste-à-Temps et flux tirés : La vision «orientée client» et la logique du «juste à temps» que promeut le Toyotisme depuis 1964, poussent les industries à passer d’une organisation de flux poussés à flux tirés. Cette évolution transforme durablement la logistique en regroupant les métiers de la logistique amont d’un côté et ceux de la logistique aval de l’autre. La tendance à la minimisation des stocks devient la norme. L’approche Juste-à-temps et les méthodes associées comme l’utilisation des boucles Kanban est une première réponse aux limites du MRP : sa sensibilité aux faibles perturbations, appelé l’effet «coup de fouet» («bullwhip effect»).
→ C’est l’émergence d’une approche globale
1983 > 2000
- 1983 :
– S&OP : Dick LING invente le processus Sales & Operations Plan (S&OP) qui consiste à coordonner les activités de toutes les fonctions de l’entreprise. L’objectif est de s’accorder sur un plan agrégé de mise à disposition de ressources pour faire face à des scenarii de prévisions de la demande à moyen et long terme.
Un S&OP réaliste exprimé en prévision de volume mensuel par famille de produit, permet ensuite d’élaborer un Programme Directeur de Production (Master Production Schedule) fiable par référence de produits finis à fabriquer. - 1984 :
– Théorie des contraintes : Développée par Eliyahu Goldratt en 1984, elle met en évidence les caractéristiques non-linéaires des chaines logistiques dans lesquelles la vitesse du flux dépend de la «capabilité» du maillon le plus faible. - 1988 :
– Méthode Lean : Dans la continuité du Toyotisme, de l’approche juste-à-temps, des boucles Kanban, cette méthode se construit autour de la recherche de la performance globale, par l’amélioration continue et l’élimination des gaspillages, afin d’améliorer la valeur globale pour le client. Le développement du Lean Management avec les notions de «Valeur Ajoutée pour le client» et de «sens du travail pour tous» accompagne l’évolution de la Supply Chain. - 1990 :
– Enterprise Ressources Planning (ERP) : Apparition progressive des ERP comme intégrateur complet des fonctions de gestion de l’entreprise comme les MRP le permettaient pour les fonctions production. L’ERP couvre bien plus que la Supply Chain. - 1991 :
– Création du terme Supply Chain pour désigner l’étendue de la chaine logistique : depuis les fournisseurs des fournisseurs, jusqu’aux clients des clients. - 2000 :
– Puces RFID : Inventées dans les années 80, l’utilisation des puces RFID se développe. Elles sont utilisées pour stocker des informations sur les produits tout au long de la chaine de production.
– Advanced Planning Scheduling (APS) : Apparition des APS, qui sont des couches de logiciel supplémentaires, complétant les ERP et ayant pour but de combler les lacunes rencontrées en gestion de production. Avec le recul, ces logiciels n’ont pas forcément répondu aux attentes suscitées.
– Développement de logiciels : De nombreux logiciels pouvant se greffer autour de l’ERP voient le jour (pour le suivi des stocks, pour les prévisions de ventes, …).
2000 > 2015
- 2000 – 2015 :
– Intermédiation : La Supply Chain est totalement transversale dans l’objectif d’être centrée sur la satisfaction des besoins clients. De nombreuses plateformes se développent pour devenir des intermédiaires entre l’industrie et le client final et développer au maximum les logiques spécifiques de la distribution (diversité des modes d’acheminement, personnalisation des livraisons,…).
Le Big Data est un outil essentiel de l’intermédiation et de la gestion d’un nombre important de flux personnalisés.
- 2005 – 2015 : L’automatisation du système industriel impacte fortement les métiers de gestion de stocks :
– Automatic Guided Vehicule (AGV) : Le développement de solutions automatisées de gestion des marchandises pour la gestion des entrepôts s’accélère grâce à la maturation des technologies de filoguidage, laserguidage, optoguidage et géoguidage ;
– Les systèmes d’assistances aux opérateurs (cobot, assistance à la préparation de commande,..) sont développés.
- 2008 :
– Accessibilité élargie de l’information : En parallèle de l’automatisation, l’accessibilité de l’information s’améliore grandement (QR code, traçabilité centralisée) sur les produits et les flux. L’accessibilité des informations en interne pour tous les acteurs de la chaîne de création de valeur (outils de la mobilité, outils ERP, Internet of Things -IoT,…). L’accessibilité des informations aussi en externe pour les autres entreprises de la filière ou pour les clients.
Une accessibilité des informations qui impose de nouvelles exigences : continuité numérique, nouvelles compétences,….
- 2011 :
– Demand Driven MRP (DDMRP) : Créé en 2000 par Carol Ptak et Chad Smith, le Demand Driven Institute développe, sur la base de la théorie des contraintes, un modèle de pilotage des Supply Chain «complex adaptif» basé sur la production de la demande réelle. La mise en place de stocks tampons (buffer), comme amortisseurs d’oscillations de flux, à des endroits stratégiques des Supply Chain constitue la caractéristique principale de DDMRP (Demand Driven Material Planning). Couplé au process Demand Driven S&OP, il permet à l’entreprise de devenir Demand Driven Adaptive. On parle alors de Demand Driven Adaptive Enterprise (DDAE).
– 4ème révolution industrielle : Les outils de pilotage de gestion des flux ont été pensés dans un contexte économique où l’incertitude et la variabilité étaient relativement faibles alors que ce n’est plus le cas aujourd’hui. Les outils numériques permettent de changer de dimension dans le traitement de cette incertitude et la Supply Chain en sera grandement impactée : capteurs, traitement Big Data, cloud, blockchain, … Ces outils permettent/tront une remontée d’information en masse et une transformation en smart datas dans de nombreux domaines (prévisions de commande, …). Ils permettront également un suivi des produits en temps réel et tout au long de leurs vies (géolocalisation, aléas d’utilisation, …)
Des métiers transformés par un nouvel écosystème plus collaboratif
L’entreprise doit trouver son positionnement sur la Supply Chain globale d’un produit donné : entre l’extraction de la matière première et le client final.
L’usine en réseau est une première réponse, en réseau avec ses fournisseurs / sous-traitants et ses clients. Elle doit être capable de recomposer facilement sa chaîne de valeur, propre à maintenir la confiance et favoriser l’innovation :
– Une relation client-fournisseur repensée ;
– Une capacité des fournisseurs/sous-traitants d’un même donneur d’ordre à harmoniser leurs méthodes de travail ;
RENDRE PROACTIVE LA CHAÎNE DE CRÉATION DE VALEUR
La Supply Chain doit devenir de plus en plus flexible et agile pour répondre à l’incertitude qui devient la norme.
Numérisée et synchronisée, la chaîne se caractérise par sa flexibilité et sa modularité. Elle peut se reconfigurer automatiquement et s’ajuster en fonction de la demande. Elle s’adapte aux inévitables variabilités (prix et volumes des matières premières, aléas de l’approvisionnement, pannes de machines, fluctuations de la qualité, etc.) tout en conservant ses objectifs de qualité et de TRS* optimisés. Virtualisée et flexible, la chaîne n’est plus ancrée géographiquement. La logique de production personnalisée à grande échelle et de lignes multi-produits devient envisageable.
Source : cf. Livre Blanc Syntec numérique 2016, p 20.
*TRS : Taux de Rendement Synthétique. Il s’agit d’un indicateur qui mesure la performance machine.
Des métiers transformés par la synchronisation globale et l’optimisation des flux
L’évolution des modes de consommation a obligé les entreprises, au fil des ans, à changer de paradigme. La demande client est le point de départ et elle impact/era toujours plus le processus de planification, un processus, quant à lui, en lien direct avec la gestion des stocks.
Planification et pilotage des flux physiques, d’informations et financiers
PLANIFICATION, UN PROCESSUS A MAITRISER
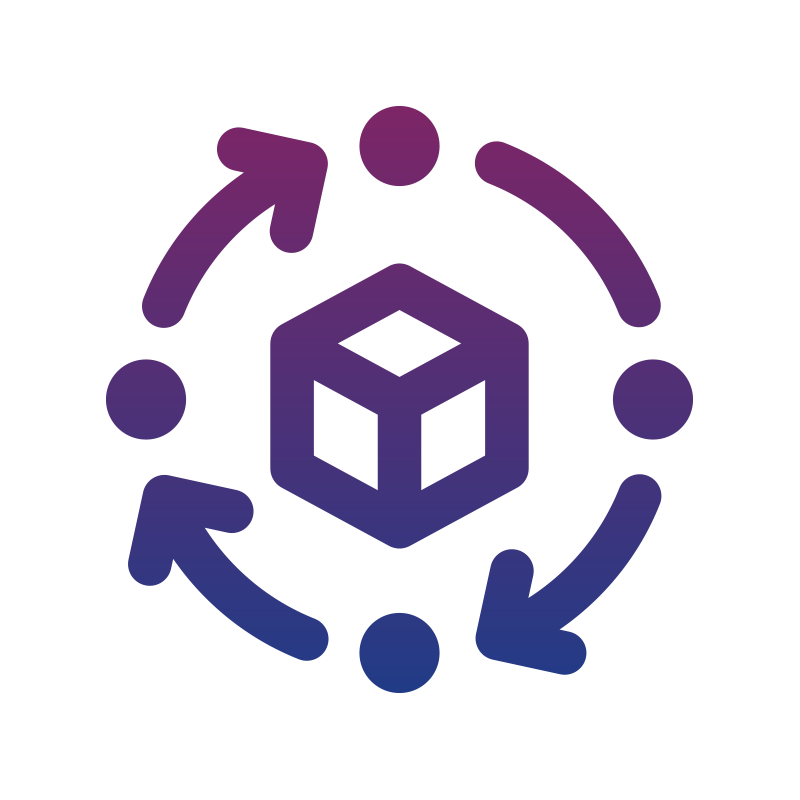
Il faut partir de la demande client, puis l’aligner sur les contraintes de la production multi-sites/multi-acteurs et aller jusqu’à la distribution avec pour objectif : la satisfaction client.
MALGRE L’EFFERVESCENCE ACTUELLE
Un processus de planification à maîtriser alors qu’il est en pleine évolution, impacté par :
– L’exploitation de la masse d’informations à disposition ;
– La planification collaborative, où plusieurs entreprises ayant besoin de produits similaires mutualisent leur planification de commande ;
– La réalimentation automatique du stock d’un fournisseur chez son client à partir d’un partage d’informations sur les prévisions de vente au client final ;
– Les moyens informatiques de traitement de données pour des prévisions court terme toujours plus difficiles à cerner ;
– L’utilisation des commandes réelles pour déclencher les ordres de production et d’approvisionnement avec une approche plus systémique complexe et adaptative, en préférant le «globalement juste au précisément faux» ;
En parallèle, les compétences de planification évoluent pour prendre en compte une planification industrielle et commerciale en ligne avec les objectifs stratégiques : au niveau corporate et pilotage Et aussi aux niveaux intermédiaires tactiques et opérationnels
EN LIEN DIRECT AVEC LA GESTION DES STOCKS
Pas de processus de planification sans optimisation du niveau des stocks pour éviter les ruptures, limiter les coûts de stockage, clarifier l’espace de travail et augmenter la visibilité des flux (pour éviter que des stocks masquent des problèmes non résolus).
Un processus de planification facilité par les nombreuses solutions à disposition :
- Gestion des stocks en bord de ligne de production
Une gestion permettant : L’optimisation de l’ergonomie de stockage I Une quantité stockée qui varie plus pour amortir les oscillations des quantités fabriquées I Une proximité avec les lignes de production plus contraignante ;
- Mutualisation de la logistique
Des plateformes collaboratives pour mutualiser et ainsi faire baisser les coûts,
d’activités tels que : La prise de commande I L’approvisionnement I Les moyens I L’entreposage I L’optimisation de transport ;
Ce sont des pratiques qui se font déjà dans la grande distribution et dans les services et qui arriveront massivement dans le monde industriel. Ainsi des entrepôts collaboratifs qui deviennent/dront de véritables lieux d’échanges qui créent de la valeur ajoutée
- Automatisation des entrepôts
La gestion des stocks au sein des entrepôts est de plus en plus automatisées grâce à : – Des chariots filoguidés (Automated Guided Vehicules – AGV) et des cabots (exosquelette, aide à la prise de commande, …) pour déplacer les produits dans les entrepôts ;
– Des outils de traçabilité (QR code, blockchain, …) pour connaître en temps réel l’état des stocks ;
– Des outils de management de la donnée (ERP, …) pour aider au pilotage des flux et des hommes, au service de la prise de décision ;
PILOTAGE DES FLUX PHYSIQUES
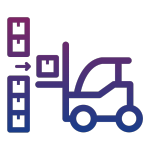
L’optimisation des flux passe par le positionnement de points de découplage entre les flux poussés, liés à la performance de la production, et les flux tirés induits par la demande client. Soutenu par la maîtrise grandissante des flux d’informations, un raisonnement par flux tiré qui n’est pas nouveau, mais va encore plus loin :
– Une théorie des contraintes plus que jamais d’actualité ;
– Une prise en compte du flux de matières premières, jusqu’ici encore peu impacté ;
– Une gestion des stocks cruciale, totalement en lien avec la demande Client ;
– Une intégration progressive de l’économie circulaire ;
PILOTAGE DES FLUX D’INFORMATION

La connexion entre flux physiques et flux d’information doit permettre une synchronisation globale de TOUTE la Supply Chain, grâce aux progrès des Technologies de l’Information et de la Communication (TIC) :
– Dématérialisation totale des échanges d’informations qui reste un chantier important pour de nombreuses entreprises ;
– Standardisation des données comme préalable à la numérisation pour en optimiser l’exploitation ;
– Traçabilité des produits en forte progression, dans tous les secteurs d’activités, notamment à travers le développement de la technologie blockchain ;
PILOTAGE DES FLUX FINANCIERS
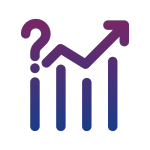
C’est-à dire que la Supply Chain aspire à être capable de chiffrer toujours plus précisément la valeur ajoutée pour le client. Concrètement, avec le rôle accru du contrôle de gestion, l’entreprise est en capacité de comprendre à la fin de chaque semaine, de chaque jour si le plan annoncé a été réalisé et si ce n’est pas le cas, de mettre en place des actions correctives.
C’est une nécessité d’intégrer des données financières dans les outils de simulation des flux, de façon à raisonner en création de valeur et cash-flow, et non plus en rentabilité machine.
Un «order-to-cash» est un outil prépondérant pour maximiser la rentrée d’argent et pour optimiser la trésorerie.
Lors de la simulation des flux, l’Intelligence Artifcielle, les outils Big data, les outils de simulation digitaux, vont jouer un rôle important pour permettre de faire des prévisions au plus près du temps réel.
- Flux financiers dans un objectif de rentabilité de l’entreprise
Quelques exemples de questions essentielles que les entreprises, surtout les PME,
ne se posent pas ou bien auxquelles elles ne savent pas forcément bien répondre aujourd’hui : - Comment valoriser la qualité de service ? Que coûte la qualité de service ?
- Quel impact financier si on s’engage à livrer quelques jours plus tôt ou bien quelques jours plus tard ?
- Est-ce qu’il vaut mieux fabriquer un produit :
– 1 fois/mois en grande quantité en optimisant ainsi les coûts de production (hors coûts de stockage), …
– 1 fois/semaine ou même 1 fois/jour en optimisant le niveau des stocks, la qualité de service, … et en recherchant plus de flexibilité et d’adaptabilité à la demande client (réduction de la taille des lots, des temps de changement de série, des gaspillages, …)
Des métiers transformés par le foisonnement technologique
BLOCKCHAIN
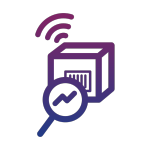
Cette technologie va permettre de :
- Repenser les collaborations dans la Supply Chain, dont les implications exactes ne sont pas encore clairement identifiée ;
- Stocker de manière fiable et sécurisée l’ensemble des données d’évolution et de traçabilité d’un produit, permettant de clarifier et de rendre transparente la chaîne de responsabilité ;
- Suivre en temps réel les produits, depuis la matière première jusqu’à l’utilisation par le client, donnant ainsi la possibilité de tracer la vie complète du produit et ses évènements majeurs ;*Ce qu’est la technologie blockchain : Bien connu dans le cas du développement des crypto-monnaies, la technologie blockchain permet de stocker de façon sécurisée l’histoire complète d’évolution d’une information. En effet, c’est une base de données distribuée (chaîne de bloc de donnée) et cryptée qui enregistre de manière décentralisée l’ensemble des transactions et des évolutions que subit un lot de données. Elle possède deux caractéristiques principales :
– Elle ne dépend pas d’un organe de contrôle car la preuve de la fiabilié du lot de données est assurée par une validation collective des usagers.
– Chaque transaction (échange/évolution) du lot de données conduit à l’ajout d’un nouveau bloc non modifiable et non supprimable validé par les utilisateurs.
SIMULATION NUMÉRIQUE
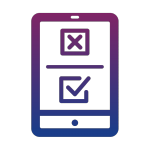
La simulation numérique et le jumeau numérique permettent de simuler l’impact de telle ou telle décision sur l’efficacité et l’efficience globale :
– Simulation de la performance avec prise de décision stratégique («make or buy») ;
– Vérification de positionnement ergonomique ;
– Simulation de transport interne ;
– Constitution des lots de fabrication (allotissement) ;
…
OBJETS CONNECTÉS – IOT (INTERNET OF THINGS)

Les lancements en production dépendent aujourd’hui d’une quantité importante d’informations, qui sont encore très largement remontées manuellement :
niveau de qualité I rebuts I temps passé, …
Les logiciels utilisés aujourd’hui traitent déjà une somme importante de données, les objets connectés permettront d’aller encore plus loin. Ces objets connectés commencent tout juste à inonder la Supply Chain et l’on peut s’attendre à une remontée d’un nombre encore plus gigantesque d’informations.
Bon à savoir : On est passé en 10 à 15 ans d’une situation où la Supply Chain manquait d’informations à une masse d’informations disponibles, prêtes à être exploitées.
Les personnes qui pilotent la Supply Chain aujourd’hui se trouvent face à une quantité massive d’informations et un grand questionnement : comment les gérer ? comment les utiliser à bon escient ? Les réponses sont encore largement à inventer et développer.
BIG DATA
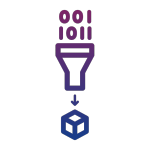
Le Big Data va :
- Aider à développer le flux d’information, pour aller plus loin que ce que permettent les ERP qui ne prennent en compte que 30 à 40 % des informations utiles ;
- Permettre de gérer une plus grande traçabilité grâce à la remontée d’informations inaccessibles jusque là ;
- Faciliter le traitement complexe de la planification et de l’ordonnancement ;
- Détecter rapidement les anomalies ;Bon à savoir : Un processus Supply Chain doit être en relation avec les métiers du Big Data pour apporter leur connaissance métier, permettant d’exploiter à bon escient les données recueilliesEn savoir plus sur le Big Data
INTELLIGENCE ARTIFICIELLE
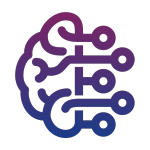
Elle n’a pas encore pénétré la Supply Chain mais va grandement se développer à différents niveaux :
- Les prévisions d’achat des consommateurs, et donc de commandes de tel ou tel produit ;
- La prise de décision par un robot ;
- La correction d’anomalies et l’auto-apprentissage ;
- Le rangement de produits dans un entrepôt. Certains experts pensent que d’ici 10 ans le rangement de produits industriels dans un entrepôt sera très largement confier à une Intelligence Artificielle. Quelques applications existent aujourd’hui dans la grande distribution ;
- Les bâtiments industriels avec la pose de capteurs permettant de mieux gérer leur consommation d’énergie, de mieux appréhender le recyclage, etc ..
Bon à savoir : Des compétences phares à acquérir : mathématiques et développement informatique
RÉALITÉ VIRTUELLE ET AUGMENTÉE (RV-RA)
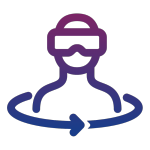
Les applications à la Supply Chain sont variées comme aide :
- À la préparation de commande ;
- Aux caristes équipés de bracelets, casques, micros pour visualiser et/ ou entendre des instructions de travail, pour valider une sortie de stock ;
- Aux tâches de contrôle dans les entrepôts ;
- À des formations ;Bon à savoir : Un constructeur automobile a développé un centre de formation où un casque de réalité virtuelle et deux commandes sont tout ce qu’il faut pour utiliser le nouveau système de formation interactif pour la logistique d’emballage. Les exercices sont conçus comme un jeu vidéo et l’équipement peut s’installer partout.
ROBOT / COBOT
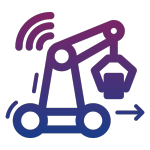
Les robots et cobots se développent dans toute la Supply Chain :
- Automates de transports internes : chariots filoguidés, éhicules autonomes. Un robot qui fait la manutention dans une zone de stockage de matières premières ou de la manutention de produits semi-finis sur un lieu de transformation, va plus vite que l’humain et peut notamment traverser des zones ou l’humain aurait besoin d’équipements spéciaux, tels que des Équipements de Protection Individuelle – EPI ;
- Robots pour déplacer des produits entre bâtiments industriels :
– à l’aide de drone pour les produits légers et de petits volumes (notamment pour les transports non planifiés) ;
– à l’aide de tracteurs automatisés équipés de robots pour les produits de grandes tailles ou lourds ;Bon à savoir : des Cobots pour aider à la manutention de pièces lourdes :
• Les exo-squelettes passifs sont déjà utilisés,
• Le co-travail d’un robot avec un humain est un axe de progrès important. Ça pose encore d’importantes questions de sécurité à ce jour De nouveaux questionnements :
– Une problématique sécurité/responsabilité largement discutée
– Un débat éthique sur le rôle du robot/cobot par rapport à l’Homme (assistance/substitution)
OPEN API
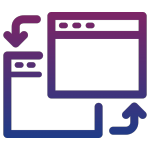
Dans l’usine connectée, les API industrielles sont essentielles pour permettre aux machines d’échanger des informations et des ordres entre elles et avec les logiciels de gestion de la donnée. Ces dernières années, parallèlement au développement des licences libres de logiciels, les entreprises choisissent régulièrement de miser sur des API publiques. Cela signifie que la partie fonctionnalités internes de l’algorithme est mise à disposition d’un public large. Cette ouverture permet une amélioration constante des API à moindre coût en contrepartie d’un risque sur la sécurité des données qui transitent ou sur la perte de contrôle de l’expérience utilisateur en interne de l’entreprise.
Bon à savoir : plus généralement, quelque soit les API dont on parle, l’harmonisation des protocoles de communication entre API est également un enjeu majeur
*À propos de l’Open API : Une API est une interface d’échange de données entre des systèmes applicatifs pour qu’elles puissent automatiquement échanger et interagir entre elles. De telles interfaces permettent aussi d’accéder à certaines fonctions internes de l’application. Les API permettent de standardiser la forme des données sortantes et entrantes entre systèmes applicatifs rendant ainsi la communication possible.
ATTENTION AUX NOUVEAUX RISQUES TECHNOLOGIQUES
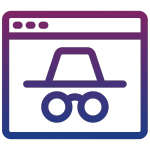
- Une perte de contrôle des données ;
- Une charge mentale nouvelle pour les préparateurs de commande qui interagissent avec des robots ;
- Être submergé d’informations non exploitables et perdre de vue l’essentiel, tout l’enjeu des traitements sera de reformater et traiter les données, pour les rendre exploitables ;
- Une cybercriminalité qui représente sans doute le risque le plus important pour les entreprises car elle peut pénétrer dans son système de données et permettre :
– de divulguer des informations confidentielle ;
– d’accéder au contenu de container pour permettre de cibler des vols ;
– d’arrêter les productions pilotées à distance ;
…
Des métiers transformés par les attentes du client final
UNE NOUVELLE EXPERIENCE CLIENT
- Respect des engagements
Partir du délai promis au client et tout faire pour le respecter, c’est le point de départ de toute réflexion globale, la qualité de service est à ce prix ! - Transparence partagée
Elle va progresser grâce au partage d’informations tout au long de la chaîne. Par exemple, nous pouvons tracer tous les aléas de production vis-à-vis du client. - Marketing enrichi
Un service transport-logistique au contact des clients qui peut devenir force de proposition sur de nouveaux produits et/ou services à développer. - Tracking complet
Un suivi du produit qui ne doit pas/plus s’arrêter à la livraison du produit, mais qui doit aller jusqu’à sa fin de vie, en passant par son utilisation. - Sur-mesure
Une approche client différencié en fonction de chaque culture / nationalité. - Client centric
Les indicateurs de pilotage de la performance sont à revisiter pour mesurer d’abord et avant tout la création de valeur pour le Client. - Mieux servir le client
Grâce au Big Data, nous aurons des prévisions d’achat encore plus fine. La technologie Big Data permet/tra de mieux gérer la qualité de service. Elle permet/tra d’analyser une grande quantité de paramètres liés au comportement consommateur pour prédire de plus en plus finement les habitudes d’achat et donc les prévisions de commande. - 3 critères à intégrer simultanément
1- Livrer à l’heure, les bonnes quantités et avec le bon niveau de qualité ;
2- Trouver le stock optimal :
ni trop, pour optimiser le coût, ni trop peu, pour minimiser le risque de rupture ;
3 Respecter les contraintes budgétaires ; - Traçabilité globale
Une traçabilité des produits et de ses composants qui devient essentielle et va permettre de TOUT connaître tout au long de son cycle de vie. Par exemple pour savoir à quel moment il faut réaliser une maintenance du produit. - Servicialisation
La vente de services, auparavant associé au produit industriel, devient le premier objectif. Cela transforme toute la chaîne de création de valeur et la Supply Chain associée, en modifiant par exemple le propriétaire du produit, les critères de suivi qualité, …
UNE NOUVELLE PERCEPTION DE LA MONDIALISATION
Les flux sont mondialisés et la Supply Chain s’approvisionne dans un environnement international, mais le seul critère du coût n’est pas opérant et la résilience de la Supply Chain est de plus en plus importante :
- Les flux mondialisés peuvent être :
+/- simple, complexe
normalisation I contraintes douanières, …
+/- bon marché, coûteux
achat + douanes + transport + …
+/- risqué
qualité I retard I respect de la commande I protectionnisme I variabilitié des contraintes douanières …
+/- acceptable
polluant I énergivore I socialement répréhensible …
- Une attente sociétale qui vise à :
– Rapprocher la production du lieu de consommation tendances «locavore» c’est-à-dire consommer local, réduction des transports. On parle de «re-shoring» ou «near- shoring».
– Porter attention aux conditions de production et de transport humaines I environnementales I éthiques…
CONFORTEES PAR L’ECOLOGIE INDUSTRIELLE
- Un management du cycle de vie des produits
– Un recyclage et une réutilisation plus optimaux grâce à un management global de la vie des produits : Une traçabilité globale de la vie des produits I Un développement du flux de retour ;
– Une augmentation de la vie des produits grâce à la «servicialisation » : c’est-à- dire du passage de l’achat d’un produit à l’achat d’un service.
- Responsabilisation
Les acteurs de la Supply Chain ont une responsabilité majeure dans la prise en compte de l’impact environnemental du fait du traitement des flux physiques. - Relocalisation grâce au progrès technologique
La robotisation, la numérisation et à plus long terme la fabrication additive (fabrication sur place, à la carte et individualisée) favorisent les relocalisations.
- Efficacité énergétique
L’optimisation des déplacements physiques amène à consommer moins d’énergie. Les bâtiments industriels sont aussi plus performants :
– Auto-producteurs d’énergie ;
– Équipés de capteurs pour mieux réguler la consommation d’énergie et moduler d’un secteur à l’autre en fonction des besoins de production ;
– Équipés pour mieux gérer l’utilisation des fluides : optimisation de l’utilisation, du stockage de l’eau, de solvants,…
L’humain au cœur des transformations industrielles
Pour appréhender ces transformations technologiques et structurelles, les équipes Supply Chain prennent de l’importance dans le pilotage des processus industriels.
La capacité à construire une vision pluridisciplinaire et systémique de ces processus est essentielle pour la transformation vers l’Industrie du Futur. La maîtrise des technologies de l’information est alors bien souvent un prérequis au pilotage d’un système complexe.
LA SYSTÉMIQUE, une Compétence clé à développer
Une vision globale systémique devient incontournable car l’optimisation globale n’est pas la somme des optimisations. Le challenge est de passer d’une approche analytique à une vision systémique. Les compétences sont doubles :
- La capacité à utiliser les Systèmes d’Information qui aident à la visualisation de la complexité de la Supply Chain.
- La capacité à construire une vision systémique.
L’approche analytique isole : se concentre sur les éléments, s’appuie sur la précision des détails, modifie une variable à la fois. Cette approche est efficace lorsque les interactions sont linéaires et faibles.
L’approche systémique relie : elle permet de travailler sur le réel, car le réel est complexe et fait système. Dans le réel, comme dans tout système, tous les éléments sont en interaction. L’action sur un élément a des répercussions sur l’ensemble du système, et tout changement global du système change à la fois tous les éléments qui le constituent et les relations entre ces éléments. Cette approche est efficace lorsque les interactions sont non linéaires et fortes.
Le macroscope, Joël de Rosnay, 1975
Évolutions des compétences managériales
- Management transversal du processus
- Un processus Supply Chain Management qui va bien au delà des métiers de la Supply Chain :
– Une nécessité de faire collaborer ensemble des personnes qui individuellement peuvent avoir des objectifs différents voire opposés ;
– Une nécessité de coordonner / synchroniser des activités réalisées par des fonctions différentes qui n’ont qu’une vision partielle des flux ;
- Équipe pluridisciplinaire
Un processus Supply Chain Management souvent animé par une équipe composé de personnes de métiers, d’âges, de niveaux de formation et de cultures différents, ayant en plus une bonne connaissance de l’anglais. - Amélioration continue
La maîtrise des différentes étapes de l’amélioration continue est essentielle. Sa mise en œuvre prend toujours plus d’importance
- Montée au COmité de DIRection
Les Supply Chain manager prennent/prendront des rôles de plus en plus prépondérants et on les trouve/era de plus en plus dans les COmités de DIRection.
Évolutions des compétences techniques
- Automatisation des flux physiques
- Une automatisation qui pénètre/trera largement tous les métiers :
– Une préparation de commande qui pourra être très largement voire totalement assistée par un robot/cobot, l’intervention humaine ne sera plus dans les rayons de stockage mais au niveau de la planification de commande ;
– Un transfert des besoins en cariste, vers des besoins en planification de commande ;
– Une montée en compétences des opérateurs pour être capable de réaliser un ordonnancement à la marge de la planification globale ;
– Un transfert de certaines compétences des cadres vers les opérateurs et techniciens : techniques de base d’ordonnancement, gestion de stocks ; - Systèmes d’information
Des métiers de base qui vont diminuer au profit de personnes qui vont manipuler les systèmes d’information.
Pour en découvrir +
Téléchargez la présentation complète de la famille de métier Supply Chain
Présentation du management de la Suply Chain, en mots simples – 2010 :
Présentation du management de la Supply Chain, en mots simples, incluant les dernières évolutions 2016 :
Un aperçu de DDMRP :
Supply Chain Manager
– Antoine, pilote de flux chez Nestlé :
Rencontre avec Maurice, assistant pilote de flux :
Responsable d’entrepôt
– Le métier de responsable d’entrepôt :
Kits de compétences
Documents à télécharger
En savoir plus sur la Supply Chain
Découvrez en détails les différents métiers de la Supply Chain
Restez informé sur l’actualité de l’AIF
Abonnez-vous à notre newsletter et Suivez les actualités de l'Alliance Industrie du Futur.